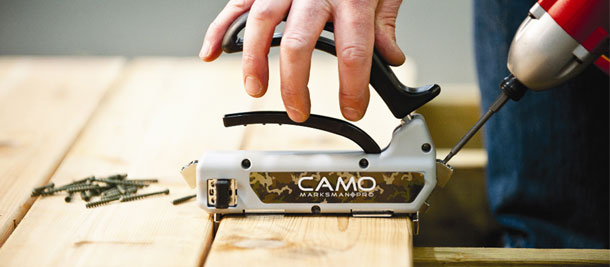
Nails vs. Screws? Face vs. hidden? Here’s what you need to know.
For many deck purchases, so much thought goes into the planks—material, color, grain—and the railings and the accessories. The fasteners, typically the cheapest and smallest product on the material list, are often an afterthought. Yet fastener selection can make just as much of a difference in the look and performance of the finished structure as the decking itself. In fact, choosing the wrong fasteners can result in stains, squeaks and painful protrusions. To help homeowners avoid these nuisances, and your builder customers avoid callbacks, help them choose the right fastener for the job. Here’s what to look for.
Materials Matter
There are many types of fasteners out there, from stainless steel and hot-dipped galvanized to nails and screws; commodity or not, what you choose makes a difference. While there are general recommendations, it’s important to match the fastener type with the material; always check with the manufacturer for specific guidelines, especially considering that using the incorrect fastener could result in a voided warranty.
Cedar
With all types of decking, especially wood, corrosion- resistant fasteners are essential. Fasteners that corrode will lead to unsightly stains, typically a blue-black mark or streak around the head. “That’s what you get when you use cheap fasteners,” notes Paul Mackie, aka “Mr. Cedar,” of the Western Red Cedar Lumber Association (WRCLA). The best option is stainless steel, which is the least likely to react with water and salt. At bare minimum, fasteners should be hot-dipped galvanized, in which the nail or screw is coated with zinc to protect it from corrosion, meeting ASTM A153. In coastal areas, always use 316 or marine-grade stainless steel.
When selecting nails or screws, there are good, better and best options: a plain-shank nail; a ring- shank or spiral-shank nail, which will hold better than a plain-shank; and screws, which are the optimal choice to ensure the boards don’t slide up and down and lead to squeaks. Screws also don’t have to penetrate as far, so shorter screws can typically be used. When installing cedar, fasten it flush; overdriving can cause water to puddle in the divot. And unlike Southern yellow pine, cedar isn’t going to shrink much after installation, so leave a 3⁄16″ to 1⁄8″ gap (or to taste) between board edges to allow water and debris to flow through.
Pressure -treated wood
Southern yellow pine now comes with several types of treatment options, the most common being copper azole and ACQ. Because of this variety, it’s important to follow guidelines from preservative manufacturers to ensure fasteners don’t react to the metals in the treatment. For its recommendations, the Southern Pine Council refers installers to Section 2304.9.5 of the International Building Code and Section R317.3 of the International Residential Code. In general, the council says, “codes require fasteners to be of hot-dipped, zinc-coated galvanized steel in accordance with ASTM A153, type 304 or 316 stainless steel, silicon bronze or copper.” The organization also reminds installers that fasteners and connectors in contact with each other must have the same metallic composition to avoid galvanic corrosion.
Composite
Because of the density of composites, most manufacturers require screws or compatible hidden fastening systems. Each brand comes with specific requirements for the types of allowable fasteners, and how and where composite planks can be screwed, so be sure to follow recommendations. One challenge that screw manufacturers have had to overcome is “mushrooming,” which occurs when the composite material coming out of the screw hole mushrooms over the screw head. Pre-drilling helps combat some of this, or mushrooms can be lightly tapped down. Newer screws, such as FastenMaster’s TrapEase, are designed to combat this phenomenon. Another hurdle has been the introduction of composite decking with a capstock, which is tougher to penetrate. Again, fastener manufacturers are responding with screws engineered to cut through the denser material. For example, Starborn Industries’ Cap-Tor and Cap-Tor xd have a specially engineered head designed to penetrate the surface layer, along with a triangular thread design and reverse thread section to prevent mushrooming, and an auger point tip for speed.
Hidden Options
Flush-nailing and stronger fasteners can help eliminate some of the visibility, but not all. One popular trend to limit fastener appearance is colored screws that match or blend with common deck hues. Among the multitude of options is Starborn’s Headcote and Deckfast screws, which are available in colors to match more than 100 wood and composite deck materials; a simple online tool helps dealers and installers match up brand/type to colors. Tamko offers its own branded line of color-matched screws for its composite lines, as well. Hidden fastening systems take it even further, and their availability and popularity is increasing. Most hidden systems are pricier than simply buying screws, but pay off in a more streamlined appearance. “Deck products are nicer and nicer, so it’s a shame to put a screw through the surface,” says Greg Hartman, national account manager for Tiger Claw. Some systems may take longer to install, but others may actually save time. Tiger Claw’s system, for example, uses half as many screws as traditional fastening and, since the screws are half as long, they take less time to drive in. Also, the Tiger Claw system is self-gapping. The Camo hidden fastening system from National Nail attaches wood and composite decking directly to the substructure with no required pre-drilling. The system includes a specially designed Marksman tool and driver bits.
With options like these, there is truly a fastener for every occasion, material and climate. While the choices may seem overwhelming, the breadth of fastener types available is making it easier than ever for contractors to create structures that look beautiful for years to come.