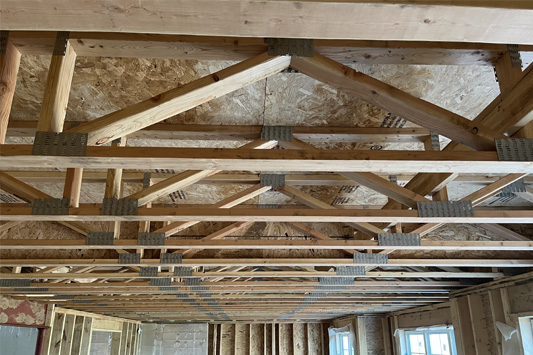
Weyerhaeuser's TJI® joists are sometimes compared to floor trusses as builders make decisions on floor systems. The floor package cost is often the primary, if not only, factor some builders consider. However, that singular focus is changing as more and more builders now consider the total financial as well as practical business impacts of switching to trusses. The result is a renewed use of Trus Joist® floor systems.
Deeper is cheaper – just not too deep
A common refrain from floor designers is “deeper is cheaper”. This statement stems from a recognition that by going a single joist depth deeper than planned (i.e. using an 11.875” floor system where a 9.5” floor system was specified), a less expensive joist series and/or wider on-center spacing could often be utilized to provide a comparable floor performance at a lower cost. And this concept still has validity in many applications today…within reason.
TJI floor systems are commonly 9.5” – 16” deep, but many truss manufacturers design floor trusses in the 16” – 20” range. It’s not uncommon to see floor trusses bid for floor systems that are several inches deeper than the TJI joists specified for that project. The deeper truss depth allows the trusses to use lower grade lumber and still be spaced 24” on-center, allowing truss designers to bid a lower price than if they were using shallower trusses that required higher grade lumber or closer on-center spacing.
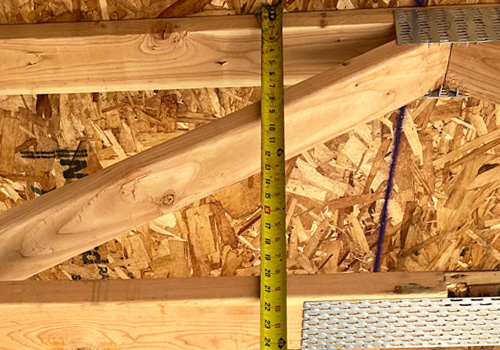
While a modest (2”) depth increase in floor height rarely has a significant impact on the rest of a home, builders recognize other costs associated with larger floor depth increases. Exterior wall finishes, amount of wall sheathing and drywall, increased garage stud heights and volume of insulation needed are some common areas where builders find extra expense linked to the deeper floor truss system. Additional costs linked to stairs (added tread/riser inside, more concrete in the porch outside) can also arise.
Real-World Example
Consider a recent example from a large builder in the upper Midwest market who used both Trus Joist products and floor trusses depending on the home model:
On a particular model where 18” floor trusses were used due to longer spans, the builder was looking to lower costs. A Trus Joist Territory Manager (TM) consulted with the builder and an additional bearing was able to be added in strategic areas that allowed for 11.875” joists to be used without sacrificing design or performance. After analyzing costs for both options (including the added footings, wall and beam) the builder and TM determined the 11.875” floor system cost was favorable.
The builder and TM then looked at data from a floor depth comparison calculator based on current material costs and the perimeter of the home, adjusting for the change from an 18” floor height to the proposed 11.875” floor system. When factoring in costs related to floor depth alone the savings from decreasing the floor system to 11.875” was $820! By reducing the height of the structure, the amount of closed cell spray foam insulation (common in that climate) was lowered, one less stair tread was needed, more than a square of siding was eliminated, garage wall studs were reduced from 12’ to 10’, and a few sheets of OSB wall sheathing were removed. The costs of the 2x4 ribbon board and 2x6 strongbacks used in the floor trusses (costs that are traditionally not included in the truss price) were also added in for a true net cost comparison. With over $800 in savings by using a shallower depth floor system combined with the net lower cost of the Trus Joist products (including the added footings, beam and wall), the savings from using a Trus Joist floor system was simply too large to be ignored.
By accounting for all costs associated with deeper floor systems versus just comparing the floor framing costs, the builder was able to capture significant savings and a competitive advantage by changing the floor system to a shallower Trus Joist floor system than deeper floor trusses.
Architectural and construction considerations
Cost savings is not the only reason to consider a Trus Joist floor system over floor trusses. In both residential and commercial construction moving to a significantly deeper floor system isn’t always a straightforward substitution. Sometimes the added floor depth not only means an extra tread and riser, but it can also lead to shifting other framing to get the required minimum ceiling heights and landing sizes at the stairs. Additionally, some jurisdictions have maximum building heights that can be exceeded as taller floors push the building higher level by level.
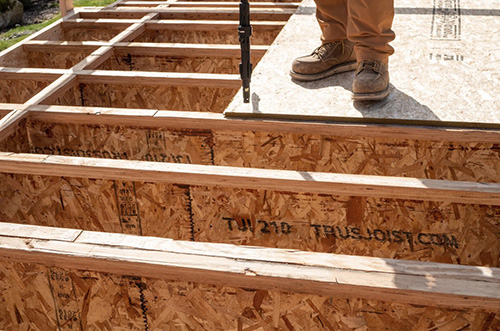
Confidence and convenience
Using a TJI floor system provides ample benefits when compared to floor trusses.
- TJ-Pro Rating System: During the design stage, floor designers can use this proprietary tool to choose the level of floor performance suitable for the project and customer, going well beyond the reliance on code prescribed deflection ratios dating back to the days of plaster.
- Lightweight: TJI® joists are lighter than trusses, making it possible for a single framer to move even long length joists.
- Long Lengths: Available in long lengths, TJI joists can run continuous over dropped beams and walls, leading to faster construction and less deflection in the floor system.
- Simplified Construction: There's no need for draft-stopping, strongbacks, or ribbons when using TJI joists. The joists (manufactured in a factory that is audited both internally and by an independent 3rd party) can be relied on to be uniform in size from piece to piece and job to job.
- Versatile Hole Locations: While trusses have natural openings between webs, contractors must adjust their mechanical runs to fit those openings. TJI joists can accommodate mechanical holes up to 24” wide, providing the flexibility to custom locate holes to align with desired locations.
- Product Availability: TJI® joists are in stock, allowing for quick delivery without the need for production lead times.
- Field Trimmable: Sometimes mistakes happen: a foundation is off or a truss is dropped or backed over by a truck at the jobsite. In case of mistakes or changes, field-trimmable TJI's can be easily adapted, and you can simply order more pieces without the need for new pieces to be “worked in” to a production schedule.
- Damage Evaluation: Another area where TJI floor systems outperform floor trusses is in evaluating damage after installation. Several frequently referenced Technical Bulletins for common problems like a notched top flange and Weyerhaeuser’s free ForteWEB® software can be used for evaluating floor framing members that were damaged after installation. Weyerhaeuser technical support is available to help and its team of engineers strives to resolve the majority of issues within 24 hours.
- Lifetime Warranty: TJI® joists come with a lifetime warranty, providing peace of mind for owners. Weyerhaeuser's team of engineers continues to provide technical support beyond product installation, including design information on legacy products for future remodeling and adaptation to modern trends like new rooftop units, solar panels, etc.
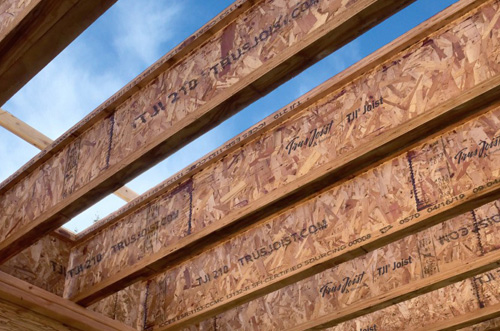
Trus Joist floor systems: the preferred solution
Once the total cost and architectural, construction, and other practical impacts to build with TJI floor joists is weighed against floor trusses, the decision to use TJI joists becomes easy for builders. Having the ability to get support quickly for field issues and hand an owner a lifetime warranty document at close further enhances the value of TJI floors, providing further separation between TJI floors and floor framing competitors.