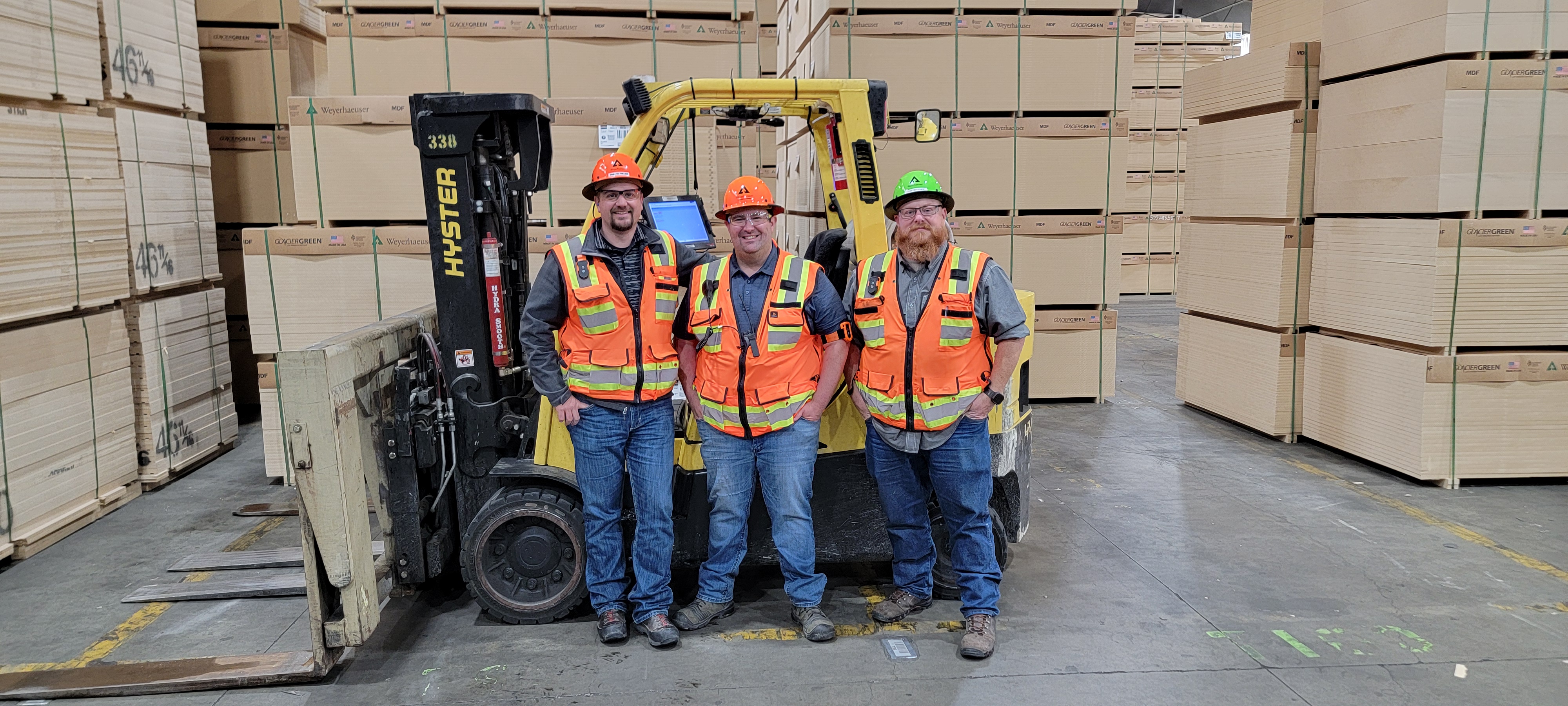
Left to right: Travis Fields, operations manager; Jordan LeFever, Lumber Safety Liaison; and Mike Butzlaff, shipping supervisor.
For the third year in a row, our medium density fiberboard (MDF) mill in Columbia Falls, Montana, has won the annual Composite Panels Association Safety Innovation of the Year. In doing so, Columbia Falls — our only MDF manufacturing facility and the longest-running MDF plant in the world, celebrating 50 years later in 2024 — beat out facilities from 34 other CPA members eligible for the award.
“That’s a lot of innovation coming out of a single team,” says Jordan LeFever, safety liaison and former Health & Safety manager at Columbia Falls. “Columbia Falls stands out thanks to a culture that encourages innovative thinking, collaboration and listening to different perspectives. Not to mention we have some of the best minds in the industry working here.”
This latest award-winning innovation is called the Proximity Alert Warning System (or PAWS), which notifies pedestrians and mobile equipment operators when one or the other may be encroaching on the ‘10-foot rule’ of safe proximity. Implemented in March 2023, the PAWS system has two parts: one sensor mounted inside forklifts and another sensor worn by pedestrians. The team says the best part of the system is its ability to identify and notify users of the presence of mobile equipment or pedestrians around blind corners and through large stacks of product.
“We had to come up with a solution to effectively address our biggest limitation: a very tight space,” Jordan says. “Columbia Falls is a 50-year-old facility, and it wasn’t designed to separate people from mobile equipment. The PAWS system works great, it’s economical, and it’s easy to implement.”
AN INCLUSIVE SAFETY CULTURE
As Weyerhaeuser’s sole MDF mill, Columbia Falls doesn’t have much room for error. Downtime, equipment failures and safety incidents can be crippling, especially considering Columbia Falls is the only Process Safety Management facility in the business — meaning it has an additional safety responsibility to the broader community to safely store and use the chemicals needed for the MDF process.
“There was an explosion at the site in 2014, which significantly impacted our business,” says Travis Fields, operations manager. “It was a real eye-opener in terms of risk tolerance. We set out to change our safety culture, and it has evolved dramatically since then.”
Innovation at Columbia Falls starts with freely sharing ideas among all employees. The site’s Safety Innovations team, which consists mostly of hourly workers, meets regularly to discuss both problems and potential solutions.
“We have new employees joining our team with novel ideas borne of video game culture,” Jordan says. “That’s why it’s so important to involve absolutely everyone. Never assume one person’s perspective is more valuable than another, regardless of their age or level of expertise.”
Site leaders also put an emphasis on talking to people every day about how safe and comfortable they feel on the job. They ask questions such as: Is there anything about your job that makes you nervous? Are there parts of your body that hurt from repetitive stress?
These conversations are key to finding hazards or risks that might otherwise go overlooked.
Some of the supporting material the team submitted about the PAWS innovation for the Composite Panels Association Safety Award, which judges on criteria such as ease of replication and effectiveness. The CPA has 140-plus members overall, with 34 eligible for the annual Safety Award. Together, members represent 92 percent of the manufacturing capacity of composite panels in the United States, Canada and Mexico.
FROM THE DRAWING BOARD TO REALITY
After identifying mobile equipment-pedestrian interactions as one of their highest risk points, the Columbia Falls team made a list of ideas to address it. Mike Butzlaff, shipping supervisor, brought insight into the challenges in that area.
“We always start with the hierarchy of controls, from most to least effective: elimination, substitution, engineering controls, administrative controls and personal protective equipment,” Travis says. “In this particular case, elimination and substitution just weren’t possible due to the existing warehouse layout. Everyone working in that area is very aware of our mobile equipment and warehouse layout, but that’s not failsafe. We wanted something more to ensure there’s no risk while our shipping department is loading railcars. Mike realized something as simple as an extra reminder could do the job. He had heard of the PAWS system and wanted to try it.”
A SIMPLE SOLUTION
When a forklift equipped with a sensor gets within 12 to 15 feet of a pedestrian wearing the small, rechargeable fob, both get notifications in the form of beeps and vibrations, plus a visual warning indicator for the driver. The driver responds by immediately stopping the forklift and lowering the forks and load to the ground. The sensor range is adjustable, which allows sites to adjust sensitivity to site-specific variables.
Cody Papa, former Health & Safety manager, helped everyone understand the capabilities of the technology and how to use it.
“By now nearly every forklift operator has said the PAWS warning saved them from potentially getting too close to a pedestrian at least once,” Cody said. “Thankfully, we haven’t had many incidents or near-misses in this area in years. PAWS has had a ripple effect of heightened awareness, even for people who aren’t wearing the beacons. That’s a big win.”
The Columbia Falls team says the PAWS system could be useful for any site with a potential for mobile equipment and pedestrian interactions.
“We highly recommend giving it a try, or finding a similar system that works for your particular conditions,” Travis says.
READY TO WIN YET AGAIN
Naturally, the Columbia Falls team has another innovation in the queue to submit for a new CPA Safety Innovation of the Year. It’s a multi-million-dollar robotic package line upgrade that eliminates some of the high-risk tasks that currently put strain on employees’ bodies.
Manufactured by Con-Vey’s 7robotics company, the automated material handling equipment will place protective cover boards around stacks of product to protect it during shipment. This process is usually done manually, which requires a lot of repetitive bending that can lead to strains and push-pull injuries.
“It’s a big investment, and it’s going to represent a massive improvement in our safety culture,” Travis says. “When we implement the system this fall, it will help ensure our team is safe and will dramatically reduce the number of times an operator has to ’touch’ a panel in the process. Of course, we also hope it will help us win safety award number four or five down the road while showing the industry how innovation and safety go hand in hand here. The awards are awesome for the team, but the biggest reward is knowing we’re making a difference and demonstrating safety systems that may help keep teams at other facilities safe as well.”