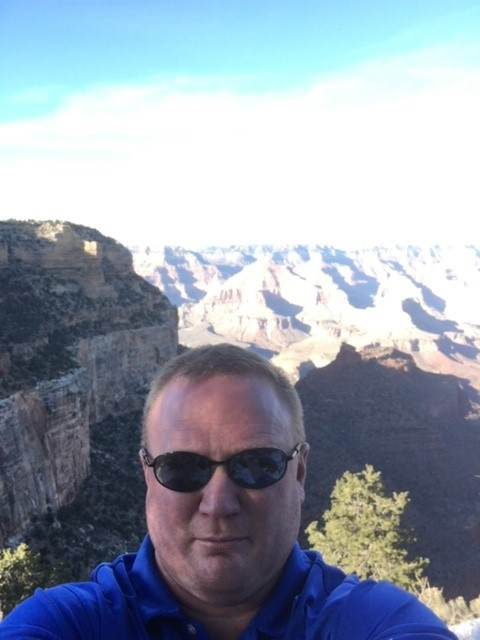
Mike Stalnaker, reliability manager at our engineered wood plant in Buckhannon, West Virginia, on a trip to the Grand Canyon in 2017.
For some, innovation can feel like a lightning bolt, a sudden flash of clarity or inspiration for a great idea. For others, innovation is more like a million tiny steps that lead toward continuous improvement and greater efficiency over time.
Mike Stalnaker fits squarely in the second category.
“I like to work smarter, not harder,” says Mike, reliability manager at our engineered wood plant in Buckhannon, West Virginia. “It’s been my philosophy since I was a kid. My parents were hard workers, and I was an only child. I learned early on the quicker I could get something done — and done right — the more free time I had to do the things I enjoyed, like hunting, fishing or hanging out with my friends.”
That "work smarter" attitude has served him well at Weyerhaeuser, and he sees innovation and process improvements as the keys to making peoples’ jobs easier and keeping them safer.
“If there’s anything I can do to make things simpler for myself or someone around me, I'm all for it,” he says. “But I also know that you need to put in effort on the front end to make something easier and more effective on the back end.”
For his ongoing efforts to continuous improvement and building a culture of innovation at Buckhannon, Mike was one of five recipients of our 2022 Innovator of the Year Award. Launched in 2021, this annual award recognizes and celebrates employees who are driving improvements and fueling operational excellence through their ideas, actions and the innovative environment they help create on their teams.
“Mike is a strong innovation leader with a passion for improvement,” says Brian Chaney, vice president of Engineered Wood Products and Innovation. “Not only has he been a key contributor to the development of a benchmark innovation culture at our Buckhannon EWP plant, he’s also been instrumental in supporting many of our companywide innovation tools and reports.”
EVERYDAY IMPROVEMENTS
A long-time leader of the Buckhannon Innovation Team, Mike has played a significant role over the last decade in shaping Buckhannon’s renowned innovation culture, which empowers everyone to continuously improve the way the team works and stays safe.
Some of his accomplishments are directly measurable: For example, in 2022, Buckhannon had 99 percent participation rate in CuttingEdge, with 151 ideas implemented and $1.3 million in value delivered.
Mike was involved with the original development of our CuttingEdge innovation tool, and he’s currently training Buckhannon’s next Innovation Champion. Buckhannon was one of the first sites to pilot the tool, and the team continues to have an impressive participation rate.
“A key factor to our success really starts when new employees are hired,” Mike says. “They’re immediately given an understanding of their role, introduced to the CuttingEdge tool and provided with information about how they can help support our innovation culture. We also run challenges in the tool to solicit solutions to specific problems, which help get everyone engaged.”
Some of Mike’s other accomplishments are harder to measure but no less important. Mike spends much of his time working on capital projects for the mill and on day-to-day process reliability activities such as ways to improve uptime, recovery, root cause analyses and CuttingEdge training and improvement. And he works with other Innovation Champions across the company, sharing ideas for improvement and serving as a resource to other businesses.
“I sit on several companywide committees where we share innovation ideas,” Mike says. “I also work to understand processes used in other parts of the company. For example, I’ve spent time with Timberlands crews to learn about what they do. I always hope to take something back for Buckhannon and in turn provide Timberlands with improvement ideas that worked well for us and might be able to be adapted for them, too.”
WORK SMART IMPACT
Mike’s been with the company for 25 years and has seen our approach to innovation evolve over that time.
“When I first started in this position, I was entirely focused in one department,” Mike says. “Now I work all across the mill. We’ve also got more companywide processes in place and more focus on innovation and safety. I’ve found that some of the best ideas surface from employees performing their day-to-day tasks and wanting to make their job safer and more effective. My role is to provide the support to evaluate these suggestions and put them in place.”
Mike says the overall impact of continuous innovation can be felt in many ways, from improving safety in the manufacturing process to reducing costs and helping deliver on customer promises.
“No matter where you are,” he says, “innovation is a culture of improving a process by gathering and implementing ideas from the day-to-day experts. It’s really a team effort, from employees bringing forward an idea to key mill management supporting it.”
He's found it's also important for employees to know their ideas matter, that their suggestions are taken seriously — and that the "work smarter, not harder" philosophy he learned as a kid still has merit.
“In this business, we need to keep innovating or we’ll get left behind,” Mike says. “It’s continuous; we must be constantly evolving to get better. And innovation helps that happen. It’s a win-win for everyone.”