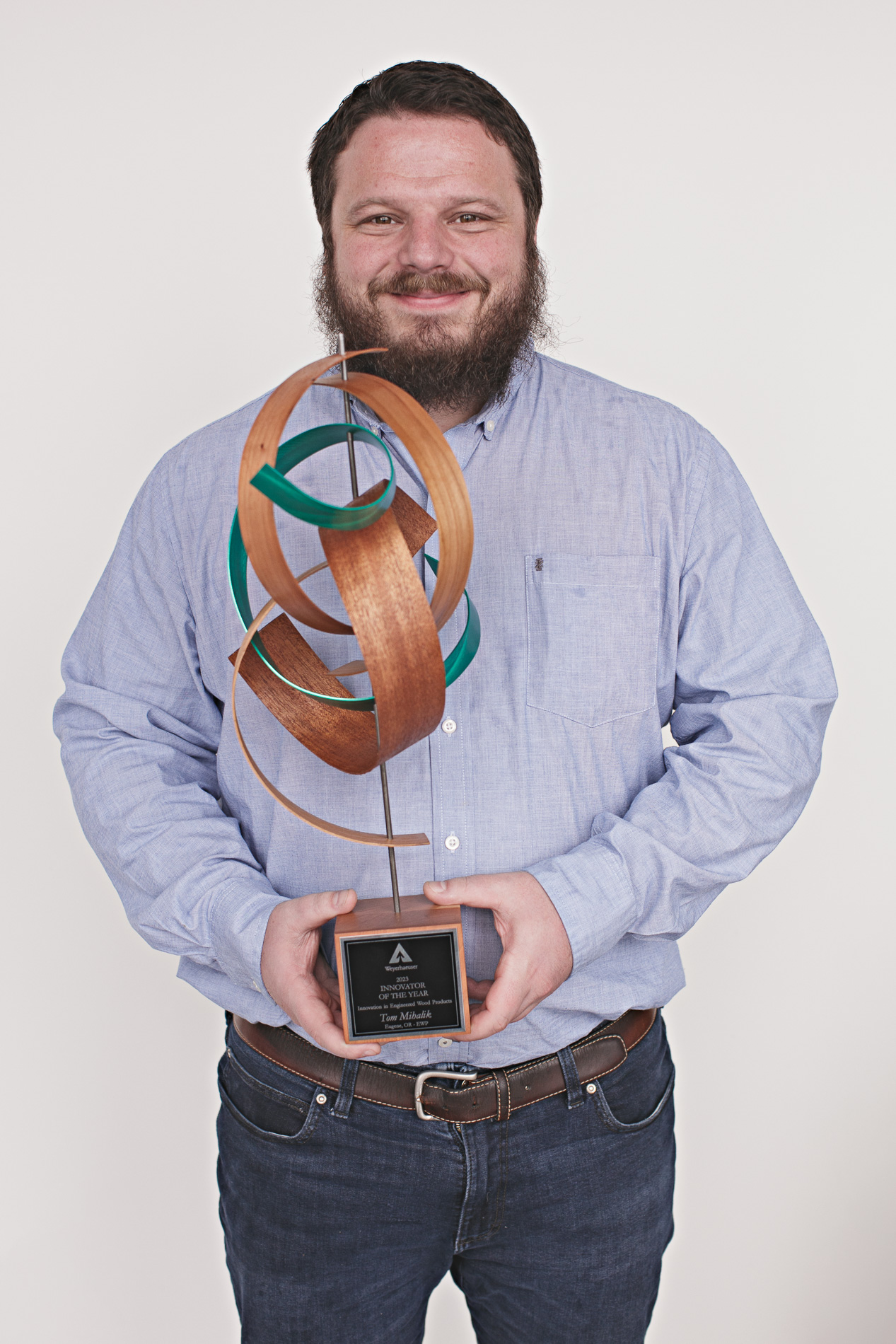
Tom with his 2023 Innovator of the Year award.
As our Engineered Wood Products plant in Eugene, Oregon, prepared for an expected market slowdown in late 2022, Tom Mihalik sought out novel ways to cut costs and improve efficiency.
“We change our shifts and production based on market demand,” explains Tom, Eugene’s technical director. “So when the market for EWP slows, there’s the possibility of taking downtime. I wanted to find a way to avoid that as much as possible.”
And he did, finding multiple ways to reduce operating costs. The first was creating a way to eliminate a costly catalyst ingredient that accelerated curing time for resins that bind the veneers in engineered wood. And the second was to deploy artificial intelligence and machine learning to fine-tune the updated recipe’s manufacturing process.
“The mill has used a catalyst to speed up resin curing for as long as anyone could remember,” Tom says. “But saying ‘we’ve always done it’ wasn’t a good enough reason to keep doing it.”
In fact, Tom perceives statements like ‘this is how we do things’ as invitations to either understand a process better, innovate, or both.
“If we don’t know why we’re following a set way of doing something, then there’s an opportunity to look at the data and either confirm the process is the best approach or find a better way,” he says.
By digging deeper, Tom’s resin and AI innovations saved the mill several million dollars last year. He also spearheaded other significant innovations related to bundle labeling and TJI Joist beam construction.
“Tom is always looking for new ideas for improvement,” says Brian Chaney, who was vice president of Engineered Wood Products and Innovation before taking over as senior vice president of Wood Products. “He helped Eugene adjust to meet changing markets and avoid downtime while creating a process change and machine learning tools that have great replication potential across our entire Engineered Wood Products business.”
For finding new practices that allow our mills to run better and serve customers more effectively, Tom was recognized as one of six recipients of our 2023 Innovator of the Year award. Launched in 2021, this annual award recognizes and celebrates employees who are driving improvements and fueling operational excellence through their ideas, actions and the innovative environment they help create on their teams.
Tom and his dog Brook take a hike in San Francisco during a recent trip along the Pacific Coast.
A PASSION FOR LEARNING
Tom joined the Eugene team in 2019 after working for six years at our OSB mill in Sutton, West Virginia. He quickly became known for his eagerness to ask questions and identify areas for improvement. He attributes his curiosity to a lifelong passion for learning, which led to his college study of wood science and economics.
“I’ve always had an innovative mindset,” he says. “Ideas tend to come to me. In this role, my focus is on quality. Which means I need a comprehensive understanding of our entire process, from handling raw materials that come in through the front door to the finished product that goes out the back door — and everything in between.”
This end-to-end perspective prompted the idea of removing the catalyst in certain situations. Specifically, Tom realized it would no longer be necessary to speed up the curing process on the press when the rest of the line was adjusted for a slowdown.
“We need the catalyst to speed things up when we need to run faster,” Tom says. “But using it constantly became inconsistent with everything else we were doing. It made as much sense for the mill as speeding up in your car for a red light.”
Tom and some coworkers participate in a polar plunge in Eugene, Oregon, to benefit the Special Olympics. The photo was later used in this ad to support the event.
THE CASE FOR CHANGE
Tom developed a proposal and presented it to the leadership team. His biggest challenge was detailing the economic benefits and proving the change wouldn’t affect quality or create unforeseen process issues.
“I think rallying people to change the status quo, especially if it involves redoing a process that’s always worked, is the hardest part about bringing any innovation forward,” he says.
But Tom’s arguments were convincing, and the catalyst was removed. Over the next several months, he deployed artificial intelligence and machine learning tools to hone the process for operating the press without the catalyst.
“We had to rebuild the entire model for operating the presses, including temperatures and pressure, because we had no history of how to run them at the slower speed,” Tom says. “AI helped us maximize press throughput and recovery. We had never used AI like this, but it was much more effective than trial and error.”
Tom recruits prospective employees with Eugene team members at the Lane County Fair.
JUGGLING OTHER INNOVATIONS
Although Tom was busy with the catalyst project during much of 2023, he also found the time to introduce other innovations, including a system to prevent mislabeling bundles that don’t meet initial order specifications. Sometimes bundles were recut due to defects but still labeled with the original specifications, which easily led to confusion in the warehouse. Tom’s simple reporting and reconciliation tool tags these bundles properly, preventing them from being inadvertently shipped to the wrong customer.
He's currently experimenting with redesigning flange connections for TJI joists, which could reduce our manufacturing costs by allowing the team to reduce the number of veneer layers used without sacrificing strength or quality.
“We still have months of trials to go, but I’m optimistic we’ll get there,” Tom says. “It’s just one more example of pushing the boundaries and challenging how something has always been done. For me, that’s the heart of innovation.”