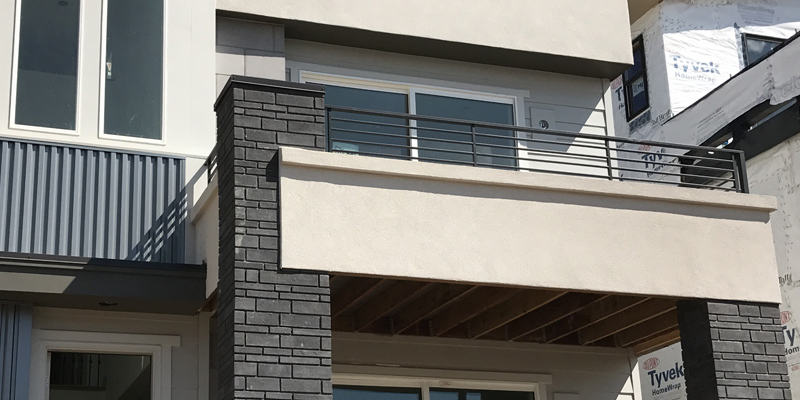
By Renee Strand, P.E.
(Referencing Applicable 2018 International Building Code Changes)
Elevated exterior building elements such as balconies, decks, and walkways are popular features for buildings and need special attention during design and construction, and throughout the life of the structure. A search on the Internet will display numerous articles that illustrate how these elements can be framed with wood and be economical, safe, and durable. One key to achieving these goals is to anticipate and design for factors that may prevent success. For example, most wood framed exterior balconies, decks and elevated walkways are intended to be protected from exposure to moisture even though the finish surface may be exposed to weather. The wood framing is protected by a moisture barrier system and designed as a dry service condition. Wood framing kept dry is durable and can provide a long service life for the structure. However, inadequate detailing, improper construction, and poor building maintenance can allow moisture to breach the moisture barrier system and intrude into the intended dry space. This situation is further aggravated where details allow moisture to be trapped, creating an environment conducive to degradation of the structural components.
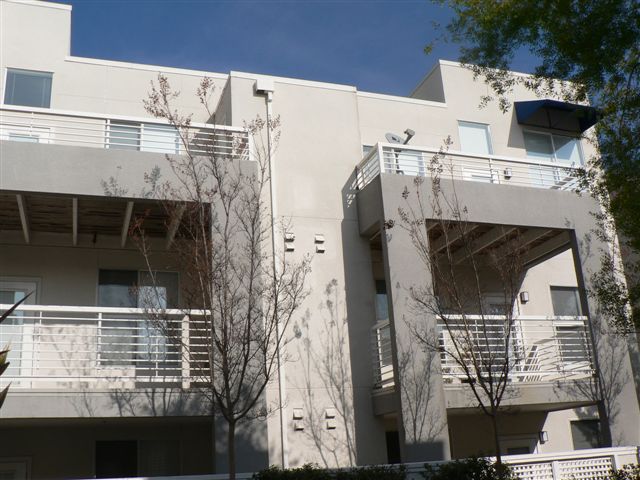
There are several positive code modifications in the 2018 International Building Code (IBC) that focus on design and protection of the structural framing for balconies, decks and elevated walkways.
- Section 107.2.5 is now titled “Exterior balconies and elevated walking surfaces” and requires detailing in the construction documents for elements of the impervious moisture barrier system when used to protect the structural framing. The construction documents are also required to contain the barrier manufacturer’s installation instructions.
- Section 110.3.6 is now titled “Weather-exposed balcony and walking surface waterproofing” and requires the impervious moisture barrier system protecting the structural framing to be inspected and approved prior to concealing.
- Table 1607.1 changed the minimum uniformly distributed live loads for balconies and decks from the same as the occupancy served to 1.5 times the occupancy served. For a balcony extending from a residential living area the minimum live load will be 60 psf (40 psf x 1.5). This change doesn’t address protection but does realign the IBC minimum design loads with the ASCE 7-10 Minimum Design Loads for Buildings and Other Structures.
- Section 2304.12.2.5 requires the impervious moisture barrier system protecting the structural wood framing to provide positive drainage for any moisture that penetrates the moisture permeable floor topping such as concrete.
- Section 2304.12.2.6 was added and requires cross ventilation for enclosed spaces of exterior balconies and elevated walkways that are exposed to moisture. Openings shall provide a net free cross ventilation area of at least 1/150 of the area of each separate space.
These code changes, once adopted by a jurisdiction, change the criteria for new balcony, deck or elevated walkway designs in that jurisdiction. Local jurisdictions may have additional requirements such as periodic inspections or the use of preservative treated or naturally durable wood for framing members. Ultimately it is the responsibility of the project design professionals to provide adequate details and instructions to ensure a safe and durable structure. Eliminating moisture issues by examining the 4 D’s;1 deflection, drainage, drying, and using durable material, is an effective way to obtain such a structure. Proper flashing, drip guards, and sufficient slope for drainage must be detailed. Provisions for allowing framing to dry if moisture penetrates the moisture barrier must be considered. Nails, screws, or bolts for deck and rail attachments that penetrate moisture barrier systems allow avenues for moisture to find its way to the framing and should be avoided. Specifying preservative treated or naturally durable wood will provide additional protection for the structural framing. Furthermore, the specification should include instructions to protect wood framing from moisture during construction and ensure the moisture content of the wood members is at a dry service condition as defined by NDS2 for the specific wood framing material, prior to enclosing. Additionally, building owners should be made aware of the importance of periodic inspection and proper maintenance to correct issues before they lead to serious problems. Detailing to enable inspection will assist this effort. Consultation with a building envelope engineering expert should be considered.
When the ability to maintain a dry service condition throughout the expected service life of the balcony, deck, or elevated walkway is in doubt, or when redundant protection is desired, a preservative treated or naturally durable wood product can be specified. Redundancy of protection is often a minor cost addition when looking at the long-term serviceability of the balcony, deck or elevated walkway. Parallam® Plus PSL (preservative treated Parallam PSL) is a possible framing option in limited markets. Check with your local Weyerhaeuser representative for sizes and availability. Currently no other Trus Joist products can be pressure preservative treated.
- D.G. Hazleden and P.I. Morris, Designing for Durable Wood Construction: The 4Ds (National Research Council Canada 1999)
- American Wood Council, National Design Specification® for Wood Construction, 2015 Edition, (Copyright 2014)
RENEE STRAND, P.E.
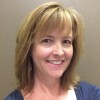
Renee Strand, P.E. is a Sr. Engineer based on out of Sacramento, CA and manages the west engineering team. She is a civil engineering graduate from California Sate University, Sacramento. During her 30 years with Weyerhaeuser, Renee has provided technical support for Trus Joist products for residential, multifamily, schools, and light commercial projects in Western US markets.