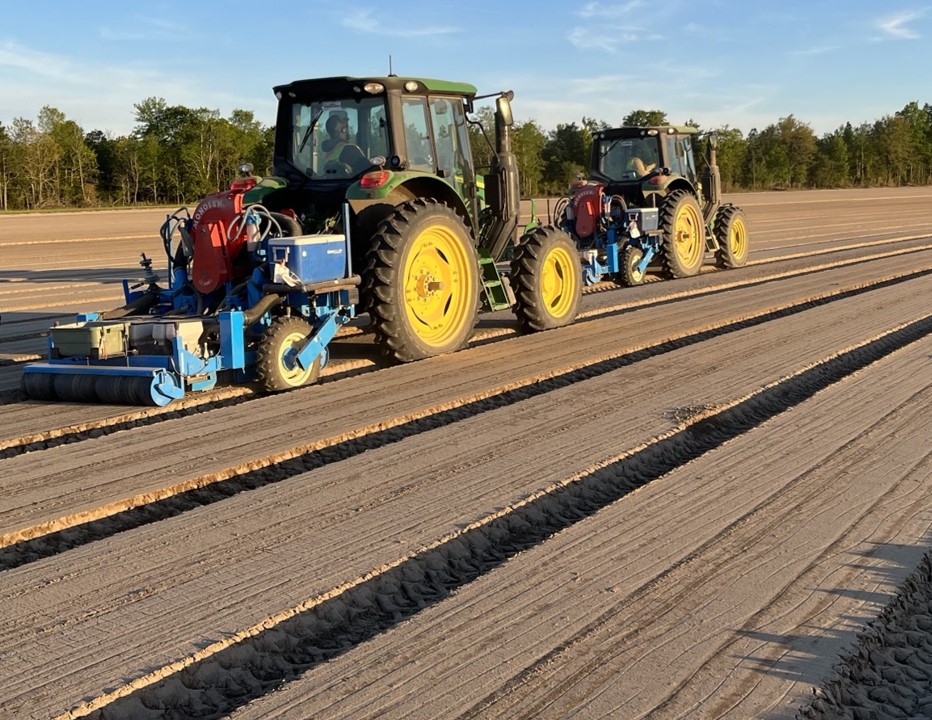
Cory Johnson (from Magnolia) and Jazmine McGinnis (from Aiken) operate vacuum sowers to precisely plant seed into the bed top. Aiken sent five employees to Magnolia: John Makekau, nursery supervisor; Richard 'Dale' Fisher, nursery production specialist; Marquess James, nursery production specialist; Jazmine McGinnis, nursery production specialist; and Mills Adams, nursery production specialist. Meanwhile, the three employees who stayed behind at Aiken did the job of eight people in their absence. They included David Scotten, nursery manager; Sheryl Wells, nursery production specialist; and Harley Gallop, nursery production specialist.
Each spring, employees at our southern nurseries face a crucial challenge: how to sow a strong crop of seedlings within a small window of good weather. A successful yearly sow sets up the rest of our internal fiber supply chain, from lifting and packing high-quality seedlings, to planting those seedlings in our timberlands, harvesting the mature trees they grow into and creating wood products from them.
“There’s no room for error,” says Alexander Hoffman, nursery manager at our regeneration site in Magnolia, Arkansas. “If we were inconsistent or had a big failure, it would push over a lot of other dominos throughout the company.”
The challenge was exacerbated for Alex and his team at Magnolia this spring with the arrival of a wave of new employees who would have to be onboarded and learn to use specialized equipment in an unusually short period of time.
Alex brought his staffing concerns to the Sow and Grow functional team, which consists of leaders from each of our three southern nurseries: Magnolia; Aiken, South Carolina; and Pearl River, Mississippi. Each site had their own goals to meet. But they realized that if they shifted some of their employees between the three sites, they’d be able to hit all their annual targets.
“The resulting collaboration between all three sites didn’t just ensure that Magnolia met its targets — it led to the most efficient sows in the history of each nursery,” says Cory Johnson, a nursery production specialist in Magnolia. “And it created benefits in cross-training, safety focus and operational excellence.”
Cory operates a vacuum sower.
LAYING THE FOUNDATION FOR OUR BUSINESS
The scale of each sow is immense, and ensuring a successful crop requires advance planning and preparation. Fields are prepped with a variety of implements to build slightly raised beds, which allow for proper drainage as the seeds grow into seedlings. Once planted, the seeds are covered with a quarter-inch of dirt, which is glued into place with a derivative of Elmer’s glue to ensure the seeds don’t float away. Then, a layer of pre-emergent herbicide is applied on top to prevent the growth of competing vegetation.
“These tasks require a lot of experienced hands on deck,” says John Makekau, nursery supervisor at Aiken. “We realized if we completed our own sowing at Aiken in a compressed time period with the help of employees from Magnolia and Pearl River, then we could send a team of Aiken employees to Magnolia. They’d get the help they needed, and everybody would get the chance to learn something new.”
In April, three employees from Magnolia and two from Pearl River arrived in Aiken for the two-week sowing period. Once complete, Aiken sent five employees to Magnolia.
“With help from visiting teams, we covered more ground each day than ever before,” John says. “It was hard work, because those of us who traveled effectively doubled the amount of time we spent on the sowing process. But it was absolutely worth it.”
Richard 'Dale' Fisher sprays a diluted glue mixture which holds the bed surface intact against rains and irrigation.
MOMENTS OF LEARNING AND CONNECTION
Much of the work the extra support staff did at each site was preventative maintenance on the machinery to ensure there was as little downtime as possible.
“A lot of the value we found wasn’t the eight-hour days in the field sitting in tractor cabs — it was the 30-minute sidebar conversations where we shared our knowledge with each other,” Alex says. “We’re all growing loblolly pine, but we have different ways of doing things that we hadn’t even thought about before. It shook us out of our preconceived notions about the ‘right’ way.”
Having fresh viewpoints on site helped to identify and fix small problems, which helped keep everything tightly coordinated.
“Aiken fills some of their tractor tires with water to add weight and lower the center of gravity, which was a big epiphany for those of us from Magnolia,” Alex says. “They gave us a great safety training to see how the process was implemented and how it improved efficiency. With water in the tires, the ripper went a little deeper into the soil, and the chisel plow was getting things a little more evened out — both benefits we could all use for our beds.”
Sunset in Aiken after a hard day’s work with curved, planted beds and a tiny lone tractor/sower. 'There’s a lot of value in getting teams together and building strong social networks, but certain opportunities really make it worthwhile to take the additional step of meeting in person when possible,' Alex says. 'I think we get multiple years’ worth of benefits in two weeks of in-person contact versus years of virtual meetings. Emails and phone calls are still happening as a result of the visit.'
EXPANDED OPPORTUNITIES FOR PROFESSIONAL DEVELOPMENT
The crew swap also offered nursery production specialists an opportunity to travel beyond their home facilities.
“A production specialist might be assigned a role in a seasonal process for three or four years to get really proficient before doing cross training,” Alex says. “This trip created opportunities to work on these processes multiple times in a single year. We did three, four, maybe even five years’ worth of cross training and developmental steps in the space of weeks.”
Cory agrees.
“The networking opportunities this collaboration offered to our new employees are invaluable,” Cory says. “When you’re just starting out, you’re still building your confidence. Everyone appreciated the opportunity to train with more experienced employees and pick their brains in a hands-on setting.”
In the future, if a similar need for swift assistance comes up, the nurseries will be ready to respond. But the teams also see other opportunities for cross-collaboration on a smaller scale, perhaps even pulling in partners from Western Regeneration.
“If there’s one big overarching lesson we all learned from this, it’s to not be too set in your ways,” Alex says. “A fresh set of eyes can bring in great ideas for safer or more efficient practices and identify hazards that might be blind spots for those of us who look at them every day. And so many possibilities for growth and improvement can arise when you work together.”