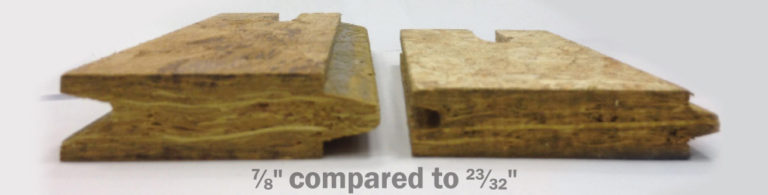
For decades, 23/32″-thick OSB has been the most commonly used thickness of OSB subflooring. But a simple switch to 7/8″ panels offers several advantages for accommodating a home’s energy efficiency and for ensuring the performance of finish materials and the overall feel of the floor.
As an increasing number of builders move ductwork HVAC systems into conditioned space, the prevalence of wider on-center spacings has also grown. The change, which is required in areas that have adopted the 2012 version of the International Energy Conservation Code, is estimated to increase a homes’ efficiency by as much as 30%.
In addition, “The beauty of 24″ on center compared to 16″ is that you effectively have one-third fewer pieces,” notes Randy Melvin, director of research and codes for Bethesda, Md.-based Winchester Homes. “The contractor has one-third fewer trips to the delivery truck, one-third fewer pieces to nail down, one-third fewer tubes of glue.”
Wider spacing, however, may lead to noticeable movement underfoot. Using 7/8″ Edge Gold OSB subfloor, as Winchester does, can help ensure performance of finished floors such as tile and hardwood while also contributing to a more stable feel. The thicker OSB also offers a 20% improvement in nail retention.
Although 23/32″ panels are span-rated for floor systems spaced at 24″ o.c., the National Wood Flooring Association (NWFA) suggests a thicker subfloor is necessary to reduce deflection of the subfloor and minimize pops and squeaks in the wood flooring. NWFA recommends a 7/8″ panel such as Edge Gold for these applications.
Similarly, tile requires sufficient stiffness. APA’s publication “Technical Topics: Ceramic Tile Over Wood Structural Panel Floors,” provides guidelines for two-layer wood residential tile assemblies; a single layer of 7/8″ Edge Gold satisfies the recommended capacity for those two-layer wood assemblies across typical joist on-center spacing. Further, compared to a 23/32″ OSB panel, 7/8″ Edge Gold is more than twice as stiff and produces less than half the expected subfloor curvature between joists, which can help prevent tile and grout cracking.
Even for resilient and carpet floors, a thicker subfloor also will feel more solid underfoot while providing additional sound dampening for multifamily applications and reducing potential damage from drywall carts during construction.
Cost comparisons show that the upgrade to 7/8″ Edge Gold results in only marginal price increases or can even reduce the cost of a floor system. “While the individual panel costs might be more, you have to look at it as a system,” notes Melvin. “You also need to factor in customer satisfaction, word-of-mouth sales. You need to consider your reputation.”